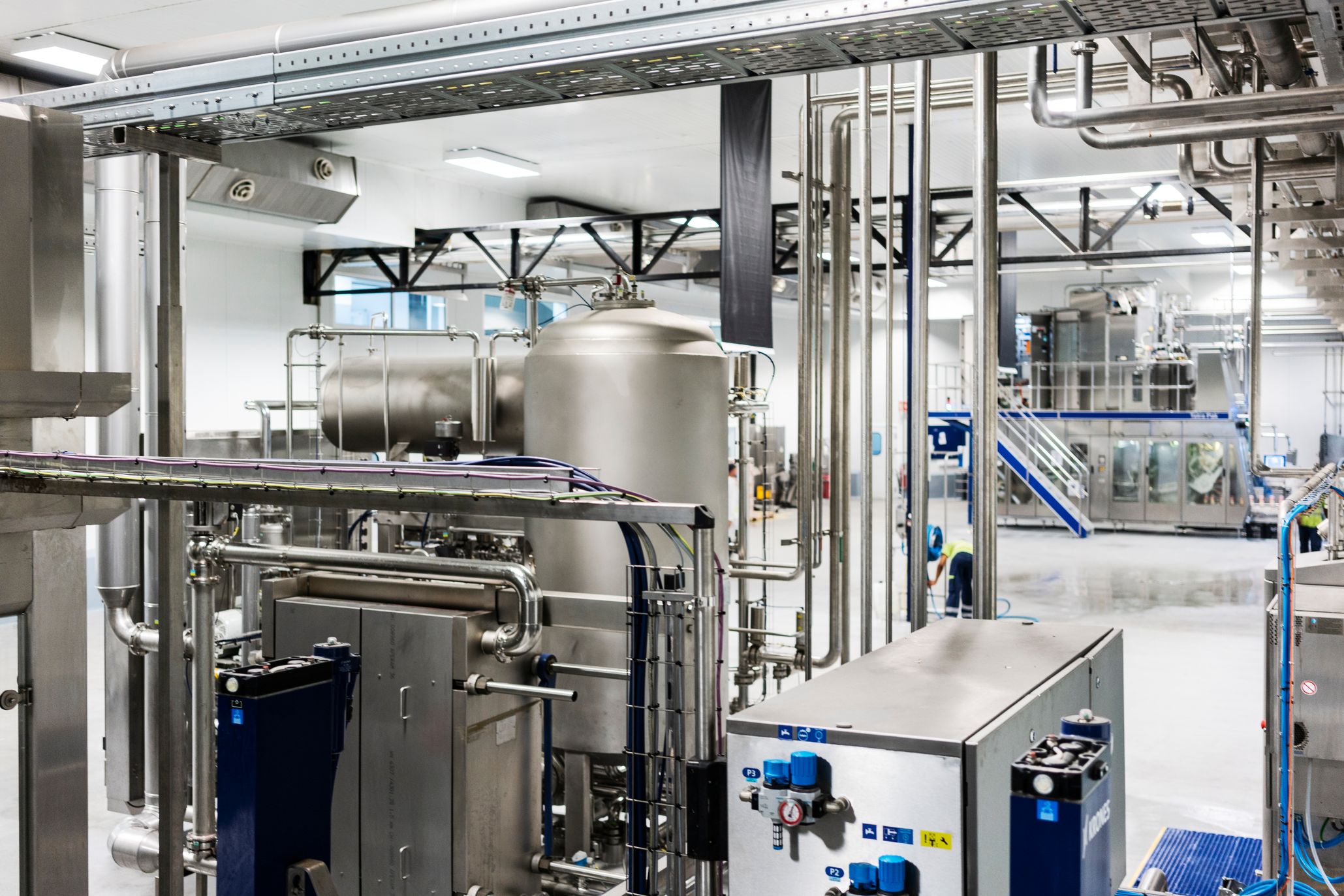
If you work in a food and beverage processing plant you probably know that your refrigeration system accounts for between 30-70% of your electricity bill - that's 50% more than you actually need to spend!
Our 5 step approach will show you how to make significant savings with little CAPEX.
Take some time to look at how exactly your plant operates and drastically increase the amount of energy your fridge plant consumes.
By dynamically controlling the system the glycol temperature can be ramped up by a couple of degrees to meet this load - saving between 10-20% easily, at no extra cost to your business!
We’ve learned, refrigeration plants are commissioned in such a way that the commissioning engineer doesn’t get a callout on the hottest day of the year when the plant can’t make its cooling capacity. This is great for production, but bad for energy consumption - but it doesn’t have to be a compromise.
When someone makes a change in your plant (suction pressure for example) do you know about it? Do you know the reason for it? And most importantly, do you know how much it is costing you?
Building on the significant amounts of data you’re now collecting, the next step is to use that data to minimise energy consumption and maximise reliability by driving targeted O&M.